Cómo controlar la aplicación de impermeabilización líquida en caliente
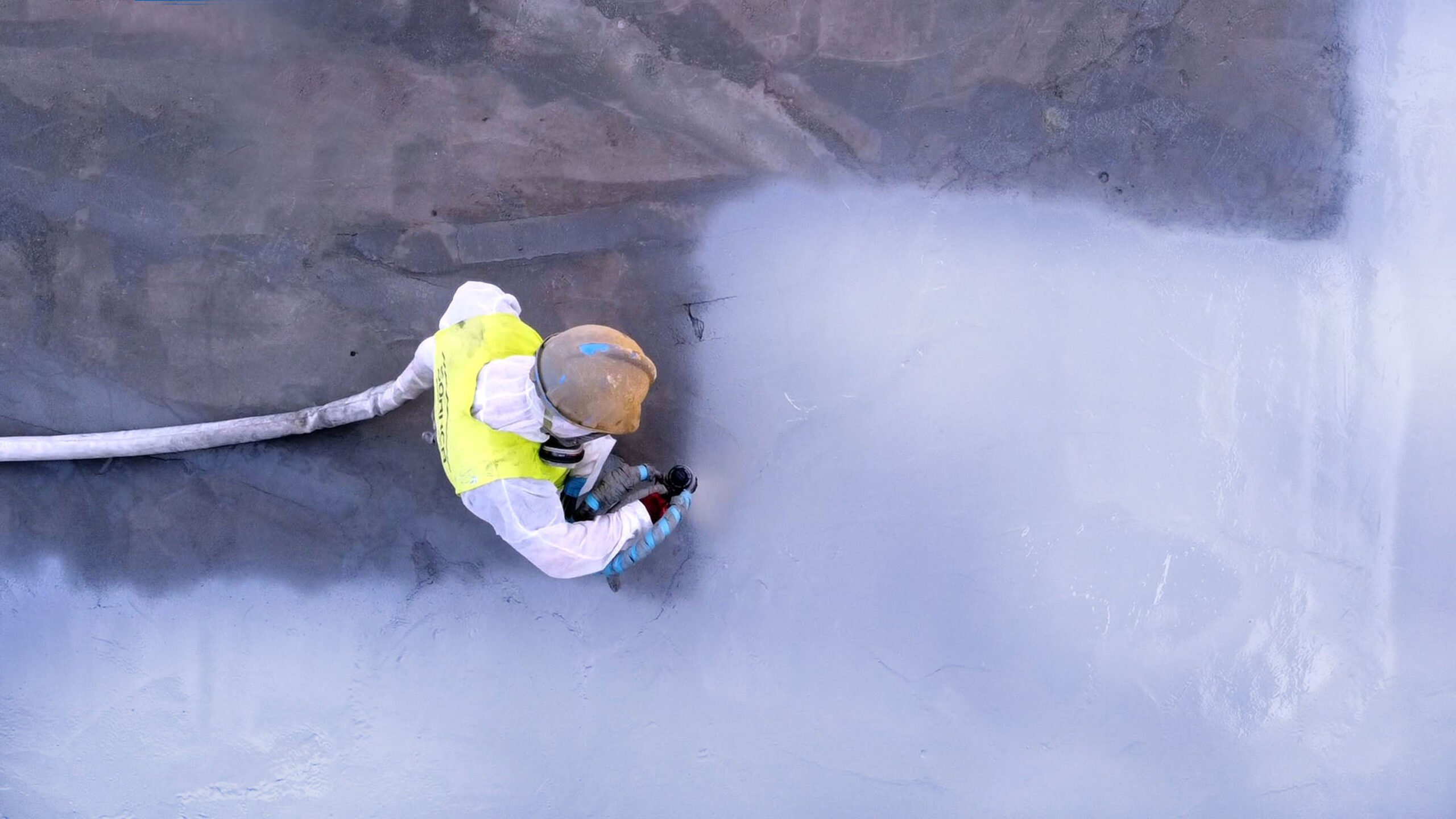
Durante el proceso de impermeabilización con membranas de poliurea o poliuretano es esencial llevar a cabo una serie de controles para garantizar la efectividad, durabilidad y seguridad del sistema, así como para prevenir escenarios futuros que puedan devenir en costosas reparaciones.
Estos procesos de inspección y control se realizan antes, durante y después de aplicar la solución conforme a unas determinadas fases:
- Controles previos a la aplicación
Antes de iniciar los trabajos de aplicación de la impermeabilización líquida, será necesario realizar las siguientes comprobaciones:
- Condiciones ambientales:
- Temperatura del soporte: entre 5°C y 35°C.
- Humedad relativa: ≤ 85%.
- Punto de rocío: Diferencia mínima de 3°C entre la temperatura ambiente y la del soporte.
- Estado del soporte:
- Adherencia mínima en hormigón: ≥ 1,5 MPa (EN 1542).
- Limpieza de la superficie y ausencia de contaminantes.
- Imprimación correctamente curada (según especificaciones del fabricante).
- Equipos de aplicación:
- Presión de la bomba y temperatura de los componentes.
- Verificación de mangueras, boquillas y caudal de aplicación.
- Controles durante la aplicación
Es recomendable establecer pautas de control mientras se proyecta la poliurea:
- Temperatura y presión de la máquina:
- Control cada 30 minutos para evitar variaciones que afecten la mezcla.
- Rango recomendado: temperatura de proyección entre 60-80°C y presión ≥ 170 bar (según especificaciones del fabricante).
- Control del espesor aplicado:
- Medición en zonas representativas tras cada capa.
- Espesor mínimo recomendado: 1,5 – 3 mm, dependiendo de la aplicación.
- Supervisión de la continuidad de la membrana
- Inspección visual de defectos durante la aplicación.
- Uso de luces rasantes para detectar burbujas o irregularidades.
- Controles después de la aplicación
Tras la aplicación del sistema completo, es importante realizar los siguientes controles para garantizar la calidad del producto y su correcta instalación: inspección visual, control del espesor, prueba de adherencia, control de dureza y prueba de estanqueidad.
Prueba de adherencia
La adherencia de la membrana a la superficie es fundamental para su eficacia, por ello se debe realizar esta prueba para verificar que el sistema se adhiere correctamente al sustrato. Es esencial que la superficie esté limpia, seca y libre de contaminantes para asegurar una buena adherencia. Los controles ayudan a verificar que se cumplan estas condiciones.
La prueba puede realizarse mediante ensayos de tracción (método destructivo: prueba pull-off), según la norma EN 1542.
Procedimiento:
- Se adhieren discos metálicos con adhesivo epoxi.
- Se aplica tracción hasta fallo.
- Criterio de aceptación: ≥ 1,5 MPa para superficies transitables y ≥ 0,8 MPa para otras aplicaciones.
Control de dureza (D Shore)
La dureza del producto se verificará de acuerdo con la norma ASTM D2240 y deberá cumplir con la dureza especificada en la hoja de datos técnicos del producto +/-5 puntos. De esta manera se puede comprobar que la relación de producto aplicada es la adecuada.
Este control se realiza antes de empezar a aplicar o después de una pausa aplicando una muestra sobre lámina de polietileno.
Control del espesor
Controlar el espesor de la aplicación es vital para garantizar que la membrana cumpla con los estándares de impermeabilidad. El espesor final de la membrana es un factor crítico, ya que influye en su capacidad de impermeabilización y resistencia. La medición del espesor final de la membrana puede hacerse con métodos destructivos o no destructivos:
- Método no destructivo: utilizando medidores de espesor electrónicos, basados en ultrasonido (soporte de hormigón) y medidores magnéticos (soportes metálicos).
- Método destructivo: cortando dos lados de un triángulo equilátero de la membrana en obra, midiendo espesor y posteriormente reparando la zona afectada.
También se puede preparar una muestra paralelamente en condiciones similares. No siempre es fácil si la adherencia es muy grande, por lo que es necesario planificarlo antes.
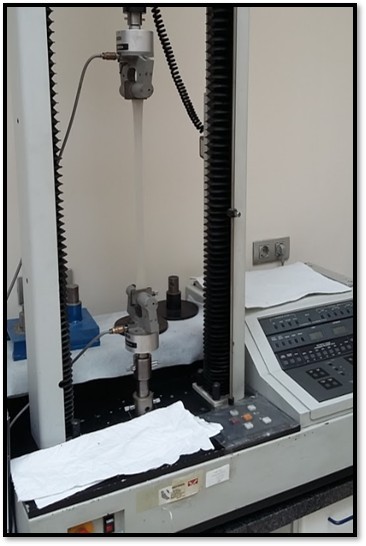
Inspección visual
Realizar controles durante y después de la aplicación permite identificar y corregir defectos, como burbujas, grietas o áreas mal cubiertas, antes de que se conviertan en problemas mayores.
Una vez aplicada la membrana, se recomienda realizar una inspección visual exhaustiva para detectar posibles defectos o áreas no recubiertas correctamente. Se deben buscar indicios de burbujas, porosidades, fisuras, desprendimientos u otros problemas visibles que puedan comprometer la calidad del sistema.
Prueba de estanqueidad
La membrana se aplica con el objetivo de lograr una impermeabilización eficiente, por lo tanto, es recomendable realizar pruebas de estanqueidad para asegurarse de que el sistema cumpla con los requisitos. Estas pruebas pueden variar dependiendo de la estructura y las condiciones específicas del proyecto, pero algunas opciones comunes incluyen pruebas de inundación según la Norma EN 1928 y pruebas de presión de agua.
Procedimiento:
- Llenado con agua a 5 cm de altura.
- Observación durante 24 a 48 horas.
- No debe haber filtraciones ni acumulaciones de agua bajo la membrana.
Se recomienda evitar hacer pruebas en secciones demasiado grandes.
Es importante destacar que estos son solo algunos de los controles, inspecciones y pruebas más comunes que se realizan en obras de impermeabilización con membranas líquidas. Cada proyecto puede tener requisitos específicos adicionales, por lo que es fundamental seguir las pautas y recomendaciones del fabricante del sistema utilizado. Un curado inadecuado puede comprometer la efectividad de la impermeabilización.