¿Cómo solucionar las patologías más comunes derivadas de una incorrecta aplicación del sistema de impermeabilización líquido en caliente?
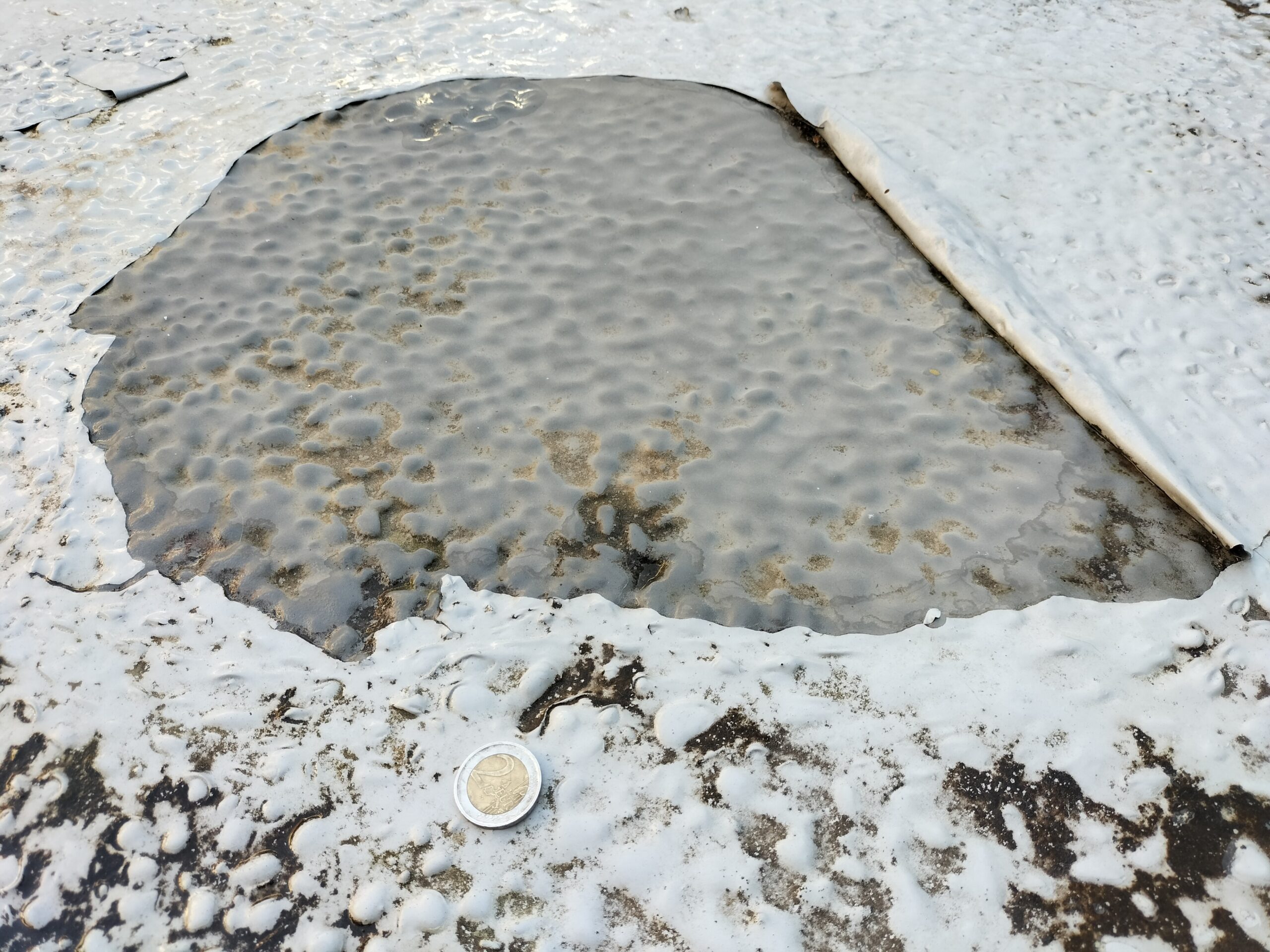
La degradación de los materiales por la acción de la climatología o por el paso del tiempo, así como los daños ocasionados por un mal uso o escaso mantenimiento del sistema de impermeabilización son problemas frecuentes en las cubiertas planas que, de no resolverse a tiempo, pueden derivar en patologías como filtraciones de agua, aparición de humedades, goteras…
Sin embargo, no son los únicos problemas que pueden comprometer la estabilidad de una cubierta a lo largo de su vida útil. En el caso de la impermeabilización líquida en caliente, los defectos derivados de una aplicación incorrecta también acarrearán problemas a medio-largo plazo. Por este motivo, es importante identificarlos y aplicar soluciones eficaces que garanticen el correcto funcionamiento del sistema de impermeabilización.
La impermeabilización líquida en caliente es un sistema de impermeabilización y protección ampliamente utilizado en la protección de superficies. Esta solución, que puede ser de poliuretano, poliurea o sistemas híbridos, se produce por la reacción química de dos componentes, que se aplican mediante pulverización en caliente sobre un sustrato, formando una membrana continua y altamente resistente.
Destaca por su rápida reacción y curado, lo que permite una aplicación eficiente y minimiza el tiempo de puesta en servicio. Además, ofrece una excelente adherencia a diversos sustratos, una gran elasticidad y una notable resistencia a químicos, abrasión y variaciones térmicas. Esto la convierte en una opción ideal para una amplia gama de aplicaciones de protección e impermeabilización en construcción e industria: desde la impermeabilización de cubiertas y terrazas hasta la protección de estructuras y depósitos. Sin embargo, una incorrecta aplicación puede genera problemas que acarrén patologías como ampollas o los conocidos como pin-holes.
“Las deficiencias más frecuentes que pueden causar patologías tienen que ver con una descompensación en la relación de mezcla, falta de presión en la máquina, problemas con la temperatura del sustrato o del producto, así como problemas con la imprimación o la preparación de la superficie de trabajo”, citan desde AIFIm. La asociación, que reúne a los principales fabricantes de sistemas para impermeabilización en edificación –ASSA, BMI-CHOVA, DANOSA, KRYPTON CHEMICAL, RENOLIT ALKORPLAN, SIKA Y SOPREMA –, subraya la importancia de realizar una correcta aplicación de este tipo de sistemas para evitar deficiencias que puedan comprometer la salubridad y el confort del edificio.
Aspectos a tener en cuenta para garantizar una correcta aplicación de la impermeabilización líquida en caliente.
1) Relación de mezcla
Mezclar los sistemas de impermeabilización líquida en su correcta proporción es fundamental para garantizar una correcta reacción química y la formación de la lámina de impermeabilización.
Para garantizar la relación de mezcla correcta, es importante almacenar los sistemas de impermeabilización en condiciones óptimas. Los fabricantes especifican de forma clara en sus hojas técnicas este tipo de factores (temperatura, humedad, iluminación, etc.) conscientes de que cualquier alteración puede provocar un deterioro de la mezcla, dando como resultado un producto gomoso, sin curar o con inconsistencias o mala adherencia.
“En la impermeabilización líquida aplicada en caliente, el frío puede ocasionar una separación de los ingredientes de la muestra. Para evitarlo, es recomendable proteger el material con nitrógeno o aire seco, manteniendo una capa sobre su superficie que inhiba la contaminación por humedad atmosférica. También es importante agitar la mezcla antes de su uso, ya que, de no hacerlo, la bomba transferirá los componentes en proporción incorrecta”, explican desde la asociación.
Además, es importante realizar un correcto mantenimiento de la máquina, revisando bombas, juntas, mangueras y pistola para evitar obstrucciones.
2) La presión.
Una correcta presión de proyección de los productos garantiza una buena mezcla y una homogeneidad del producto final. Un exceso de presión puede generar espesores irregulares, mientras que la falta de presión puede dar lugar a mezclas pobres.
3) La temperatura.
Aquí podemos encontrarnos con varios problemas relacionados tanto con la temperatura del sistema a aplicar como de la superficie donde se aplica. Por un lado, si no se alcanza la temperatura adecuada, la mezcla puede verse comprometida.
“A baja temperatura la viscosidad del material aumenta, dificultando el bombeo. También el componente B (ISO) puede crear cristales que obstruirán los filtros y válvulas. En el caso contrario, por exceso de temperatura durante largos periodos de tiempo, disminuye la reactividad del componente A y aumenta la viscosidad del componente B, debido a reacciones secundarias que comienzan a temperaturas elevadas; en este caso el aumento de viscosidad es irreversible”, argumentan desde AIFIm.
Pero también hay que tener en cuenta que tanto la temperatura del sustrato como la temperatura ambiente influyen en la correcta formación de la membrana del sistema de impermeabilización.
4) La imprimación
Este es el factor más importante a la hora de realizar una correcta impermeabilización de la cubierta. Se debe imprimar para asegurar la adhesión adecuada del sistema.
Es importante recordar que cada soporte requiere una imprimación específica. Además, no se debe olvidar que la impermeabilización líquida se ha de aplicar sobre la imprimación dentro de un intervalo de tiempo específico (ventana de adhesión), ya que de no hacerse así no se adherirá correctamente (no habrá pegado).
Estos mismos criterios se pueden aplicar a la hora de evitar problemas con el recubrimiento.
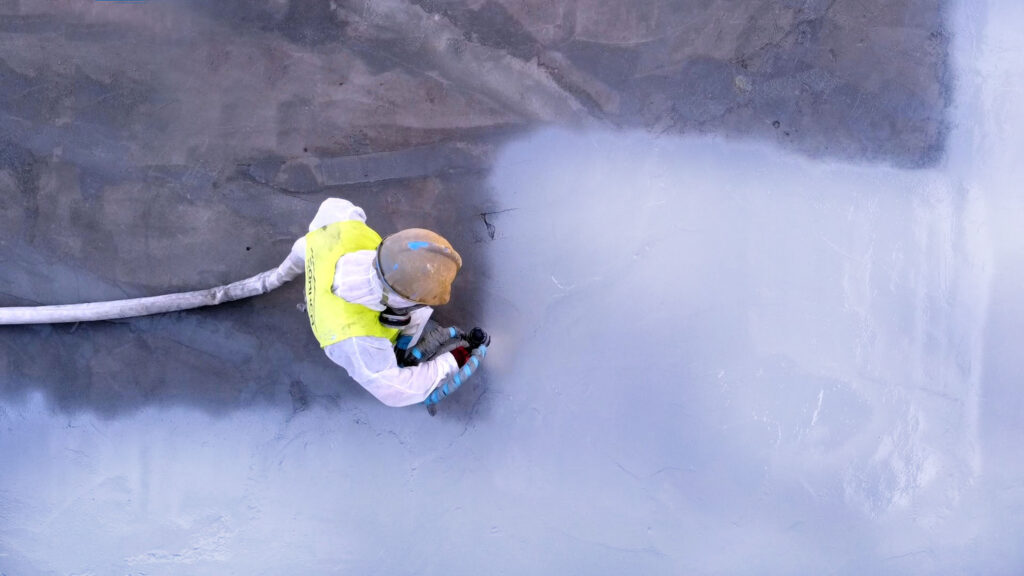
Algunas patologías y cómo solucionarlas
Una incorrecta ejecución del sistema de impermeabilización, al darse alguno/s de los problemas citados con anterioridad, puede desencadenar la aparición de patologías como ampollas, pin-holes, etc. Para darles solución es importante identificar correctamente el origen del problema.
* Ampollas de humedad.
Estas pueden deberse a diferentes condiciones: una relación de mezcla incorrecta; salpicaduras de ISO; una incorrecta configuración de la cámara de la pistola o un fallo en la unidad de dosificación; por aplicación temprana sobre la imprimación (antes de que esta haya curado); por humedad atrapada sobre el soporte, o por defectos del sustrato –por suciedad, por “efecto sombra”, por un mal recubrimiento del sustrato–.
Dependiendo de dónde aparezcan las ampollas y su apariencia, se podrán tratar de una forma u otra.
a) Ampollas que aparecen entre el sistema de recubrimiento y el sustrato. Si son suaves y sin arrugas, pueden deberse a la contaminación del sustrato o a que se haya quedado gas atrapado en su interior, en cuyo caso se recomienda una limpieza del sustrato. Sin embargo, si son ásperas o filamentosas pueden ser una reacción a la humedad o una descompensación en la relación de mezcla (exceso de ISO) en cuyo caso se recomienda secar el sustrato, revisar la temperatura de funcionamiento, comprobar las presiones y chequear el estado de la máquina de proyección para asegurarse de que está en las condiciones óptimas.
Por último, puede ocurrir que la ampolla tenga un aspecto pegajoso, seguramente debido a problemas con la mezcla o a no haber respetado los tiempos de curado de la imprimación. Comprobar la mezcla, la temperatura y las presiones, así como la máquina de proyección son las actuaciones recomendadas en este caso.
b) Ampollas que aparecen entre las capas de recubrimiento. Si estas son suaves y sin arrugas, la causa más probable es una superficie contaminada, “lo óptimo sería limpiar la superficie y aplicar una capa adhesiva”, explican desde la asociación.
Si por el contrario son ásperas o con filamentos podríamos encontrarnos ante una reacción a la humedad, “en cuyo caso habría que comprobar el sustrato, el aire seco del compresor y la temperatura y presiones de funcionamiento”, apuntan.
En el caso de una apariencia pegajosa, esta puede deberse a problemas con la mezcla (exceso de resina) y, al igual que en el supuesto anterior, lo recomendable es comprobar temperatura y presiones, así como la pistola o cámara.
* Pin-holes o puntos de alfiler.
Denominamos pin-holes o puntos de alfiler a esos pequeños cráteres que se forman en el producto durante el proceso de secado, provocando un problema estético y funcional, ya que comprometen la estanqueidad de la cubierta y su resistencia.
Entre las causas comunes de su aparición están:
a) Aire o disolvente ocluido dentro de la membrana. Cuando se aplican membranas que contienen disolventes es importante hacerlo en capas finas para evitar la aparición de pin-holes, debido a que estos disolventes son muy volátiles y tienden a ascender una vez la membrana se ha aplicado. Si la capa es fina no hay problema, los disolventes se evaporan sin más, pero si la capa es muy gruesa, además de una mayor concentración de disolventes, estos no tienen tiempo para salir y quedan ocluidos en el interior de la membrana formando burbujas en su superficie. En algunos casos estas burbujas consiguen romper la capa superficial provocando la aparición de pin-holes.
“Este mismo problema puede aparecer si el producto ha espumado o contiene aire en su interior, por lo que se recomienda agitar/batir el producto a bajas revoluciones y, a ser posible, con un agitador tipo cesta”, apuntan desde AIFIm.
b) Pin-holes por aire ocluido bajo la membrana. La aplicación de una membrana directamente sobre un soporte sin tratar o insuficientemente tratado puede provocar que el aire quede atrapado debajo de la misma.
Este aire es menos denso que el producto que lo retiene, ascendiendo a la superficie y quedando atrapado en forma de pin-hole.
En la aplicación de membranas calientes el secado es mucho más rápido por lo que podemos pensar que el aire no va a tener tiempo de salir, pero la temperatura de la membrana calienta el aire, provocando que este ascienda muy rápidamente, generando nuevamente pin-holes”, aclaran desde la asociación de fabricantes.
“En definitiva, para evitar patologías derivadas de una mala aplicación del sistema de impermeabilización siempre es necesario preparar adecuadamente el soporte y aplicar el producto siguiendo las indicaciones del fabricante, atendiendo a las recomendaciones sobre temperatura, presión, etc. Además, desde AIFIm siempre recordamos la importancia que tiene contar con el trabajo de profesionales cualificados y con experiencia”, concluyen.